Liquid Mirrors

UBC/Laval 2.7m LMT
Table of Contents
- History
Structure of Liquid Mirrors
About mercury...
History
The
The idea of using a rotating liquid to create a perfect paraboloid was
originally proposed by Sir Isaac Newton but the very stringent
requirements, in particular on the speed of rotation and leveling,
prevented any serious attempt to build a prototype before the second
part of the nineteenth century. The first published account of a working
LMT was provided by Skey (1872), who constructed a 35cm telescope, and
made the first detailed calculations of the focal length in terms of
angular velocity.
By 1909 an optical physicist, Robert Wood, published
a series of papers describing his success using a 51cm LMT. He carefully
analyzed the main sources of vibrations, and was able to obtain photographic
trails of stars. He could even resolve double stars having separations as small
as 2.3 arcsec. In order to suppress the ripples on the
surface of the mirror, he experimented with the effect of oil layers.
In spite of his success, Wood decided to abandon the LMT because he felt
that its restriction to zenith observations made the astronomical applications
too limited.
The current era of LMT research began with
Ermanno
Borra's landmark paper
(Borra 1982). He reassessed the details of the theory and practical
limitations of LMTs as true astronomical tools in light of
technological advances since Wood's time. Over several years,
the technology was developed successfully to produce a 1.5m
diffraction-limited LMT. Then, a fruitful colaboration began between
Paul Hickson
at UBC, and Borra. Hickson designed
the 3m-class LMs, and built several 3m-class LMs for UBC, NASA, and UCLA. Using this design Luc Girard (Laval) built a 2.5m
diffraction-limited LM. Hickson and collaborators are now building the 6m LZT
located at the UBC Liquid-Mirror Observatory .
Originally developed for astronomical research, LMs soon proved to be
useful in other fields of science, such as
LIDAR
science,
optical testing and
search for space debris. Certainly, LMTs do not replace the classical
instruments of astronomical research, but they are cost-effective
and they could avantageously find a niche in dedicated surveys.
For more history, see the excellent review article
and related publications by
Brad Gibson.
Structure of Liquid Mirrors
The technology of LMs is relatively simple. Three components are required:
- - a dish containing a liquid reflecting metal
- an air bearing on which the LM sits
- a drive system.
The dish
In order to reduce the amount of mercury required, the surface of the dish
matches the required parabolic shape as closely as possible. The structure of the dish depends on the diameter of the mirror. For mirrors
smaller than 2m in diameter, a simple dish spincast with epoxy or other
polymer-resin has sufficient stiffness. For many reasons, including a large coefficient
of thermal expansion and large mass density, epoxy cannot be used
for mirrors larger than 2m. The figure below shows the design for mirrors
in the 2m to 4m class.
- Structure of the 2.7m mirror (Hickson et al. 1993)
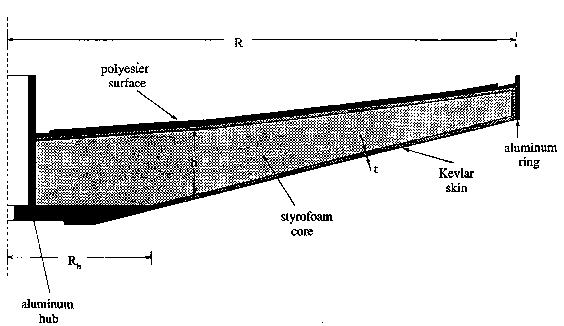
It's made of a foam core sandwich, stiffened by a Kevlar skin. A central tube
sits on a bottom plate both made of Al. The upper surface of the mirror is
spincast with an elastic resin about 1cm thick. The final deviation from a
paraboloid is less than 0.1mm.
For the next generation of LMs, i.e. mirrors larger than 4m a stiffer and
lighter design is being developed at UBC. The new design will provide a
higher stiffness-to-weight ratio and better long-term stability for such
large mirrors.
The air-bearing
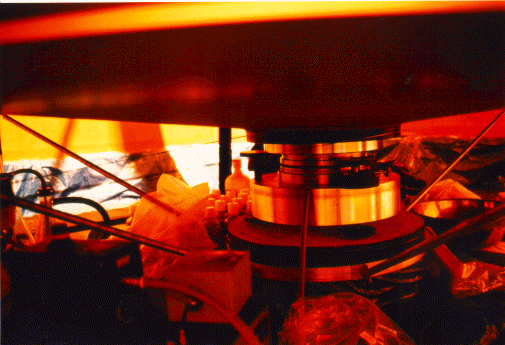
The optical quality of the reflective surface depends mainly on three
parameters: the Hg-air interface, vibrations and the vertical alignment
of the rotation axis. The third parameter implies that wobbling should
be controlled accurately. A search of available technology (late 80's),
showed that only air-bearings provided an
angular stiffness, low friction and a precision compatible with LMTs requirements.
The photo shows the bottom of the 2.7m LMT with a close view of the
air-bearing.The drive system
This component of the mirror has undergone a major evolution in its design
since the first LMTs. The drive system has to be regular (10E-6)
and must not transmit vibrations to the mirror that would disturb
the surface.The first designs used a synchronous motor linked to a
precise oscillator. The mirror was driven by a belt over a pulley attached
to its base.
This design was sufficient for a laboratory LMT but it was not adapted for
night observing conditions. The system suffered from moisture and
temperature variations.
In the 2.7m UBC/Laval LM, the belt drive has
now been replaced with a direct drive
based on a similar system developed by NASA for their 3-m LM.
The motor stator is mounted directly on the air-bearing base, and
the rotor is attached
to the rotating spindle. An optical encoder senses the angular velocity.
This new design is simpler and more reliable.
For more information on the structure of LMs:
Hickson, P., Gibson, B.K. & Hogg, D.W. (1993). "Large Astronomical Liquid Mirrors",
Publ. Astron. Soc. Pacific.,105, p. 501-508.
Hickson, P., Borra, E.F., Cabanac, R., Content, R., Gibson,
B.K. & Walker, G.A.H. (1994), UBC/Laval
2.7m Liquid Mirror Telescope, Astrophys. J. ,
436, p. L201-L204.
About mercury
Like all other heavy metals, mercury is potentially harmful for health.
Although, metallic mercury itself has not been proven to be hazardous, comprehensive
information can be found in medical publications on the
toxicity of mercury vapours and metabolized mercury oxides. In particular,
mercury oxides are thought to have
an effect on the nervous system on long time-scale. After years of
exposition to mercury vapours a series of symptoms can appear, from severe
neurologic troubles, insanity, to Parkison disease.
In addition to hazardous effects, pure mercury can be easily contaminated when
mixed with other chemical elements. It forms amagalms with almost all metals,
and consequently looses its reflective properties.
For all these reasons, one has to address the problems of mercury storage
and handling.
Some data on mercury
Atomic weight |
200.59 |
Density |
13.691 kg/l (temp. var. = 13.595 x (1 + 1.8144e-4 x T)) |
Melting point/ Boiling point |
-38.84 deg C/ 356.73 deg C |
Electrical Resistivity |
94e-8 Ohm/m |
Reflectivity |
75.8% at 400nm, 77.2% at 600nm, 77.6% at 800nm |
Surface Tension |
435.5
mN/m (at 20 deg C, in air) |
Storage: Even moderately pure mercury still has good reflectivity.
Therefore we don't need special glass containers for mercury
storage. We use plastic laboratory bottles of 500 ml. capacity. Mercury must be
stored in double or even triple containers, in order to contain a spill if a
bottle leaks or breaks. The plastic bottles containing the mercury are stored in
large plastic bins which are themselves located inside a sealed spill container.
Safety: When handling mercury, or cleaning the mirror, it is essential to
avoid
direct contact with mercury. Respiratory masks approved for mercury vapour, polymer gloves,
Tyvek lab suits and boots are used. The mercury vapour levels must be monitored
at all times.
A study was made of the mercury vapour
concentations at the UBC/Laval 2.7-m Liquid-Mirror Observatory under various
conditions.
The principal results are the following:
- Vapour concentrations inside the observatory depend strongly on the degree
of ventilation. Even a small amount of ventilation, is effective at reducing
the vapours to acceptable levels. (the Canadian legal norm is 0.05 mg/m3
on the basis of 8h/day, 5d/week exposition without protection)
- During normal operation of the observatory, in which the roof is open,
vapour concentrations are below 0.1mg/m3 for all but the first hour after
implacement of the mercury on the mirror.
- The mercury is stabilized by a thin surface layer of oxide which forms
naturally. Although pure mercury doesn't oxide alone, oxidation is catalysed
by water vapour and impurities on time-scale of a few hours. This surface
layer reduces the rate of evaporation
of the mercury by more than five orders of magnitude.
- After the oxide layer is established, vapour concentrations within the
observatory are inversely proportional to the ventilation fan capacity.
The width of the oxide layer increases constantly with time, and after
two weeks of operation, the evaporation rate is negligible.
- During startup and the first few hours of operation ot the mirror,
vapour levels in the observatory can be minimized by preventing ventilation.
High vapour concentrations are thereby restricted to a thin layer of air above
the mirror resulting in a low evaporation rate.
Hickson, P., Cabanac, R., Watson, S.E.M.,
A study of Mercury Vapour Concentrations... (priv. com.)
Links
-
LMT home
Last updated: 1999/11/13